“This is the first time this type of process has been used, and it’s unlocking new possibilities,” said Bujingda Zheng, a doctoral student in mechanical engineering at the University of Missouri and the lead author of the study.
This new method paves the way for a new generation of devices and sensors, including circuit boards and fabrics embedded with electronics.
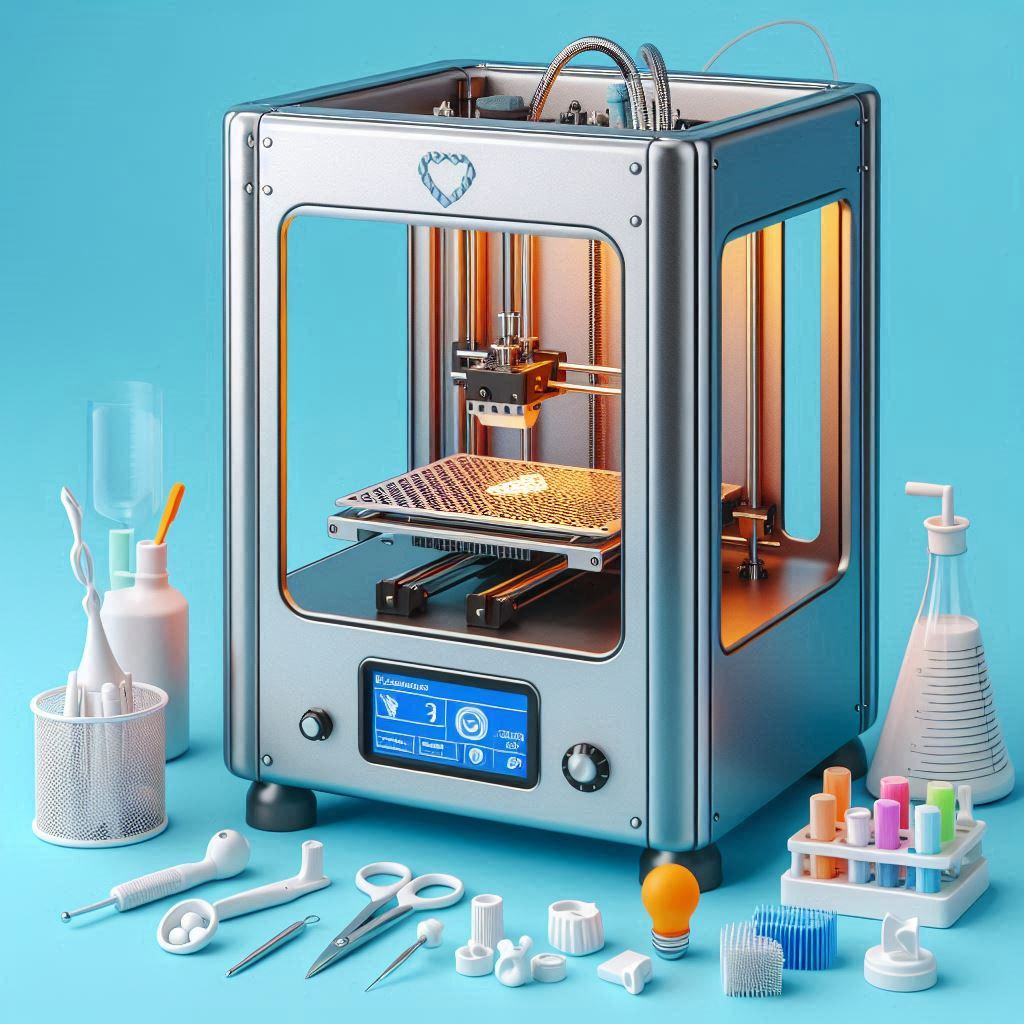
Typically, constructing complex multi-layered devices like circuit boards is a time-consuming and costly process, requiring multiple steps and different machines. This complexity can stifle innovation and slow down the development of new products.
The new 3D printing machine utilizes an innovative technique called the Freeform Multi-material Assembly Process. This process is inspired by nature and is environmentally friendly. For example, an electric eel has bones and muscles for movement and specialized cells that generate electricity. Similarly, this 3D printer integrates structural and functional materials.
“Everything in nature consists of structural and functional materials,” Zheng explained. “For example, electrical eels have bones and muscles that enable them to move. They also have specialized cells that can discharge up to 500 volts to deter predators. These biological observations have inspired researchers to develop new methods for fabricating 3D structures with multi-functional applications, but other emerging methods have limitations.”
The machine operates with three nozzles: one builds the base structure using a standard 3D printing filament like polycarbonate, a laser nozzle carves shapes and transforms parts into a special conductive material called laser-induced graphene, and the final nozzle ensures the end product is fully functional.
This new machine has diverse applications. It can print sensors directly onto rocks and seashells, allowing researchers to conduct environmental studies, such as monitoring ocean health and measuring water flow. For everyday users, this technology could lead to wearable health trackers embedded in clothing, monitoring vital signs like blood pressure and heart rate, potentially eliminating the need for bulky devices.
The developers emphasize that this technology is a game-changer for product development. Companies can now create prototypes on-site, significantly reducing prototyping time and accelerating the entire process.
“This opens the possibility for entirely new markets,” said Jian “Javen” Lin, an associate professor of mechanical and aerospace engineering at the University of Missouri.