As businesses continue to grow and expand, managing supply chains effectively becomes increasingly crucial. However, when working with the wrong supply chain agency, even the most well-planned operations can be severely impacted. In this blog, we will explore the lessons learned from such experiences and provide examples to illustrate the importance of careful selection and management of supply chain partners.
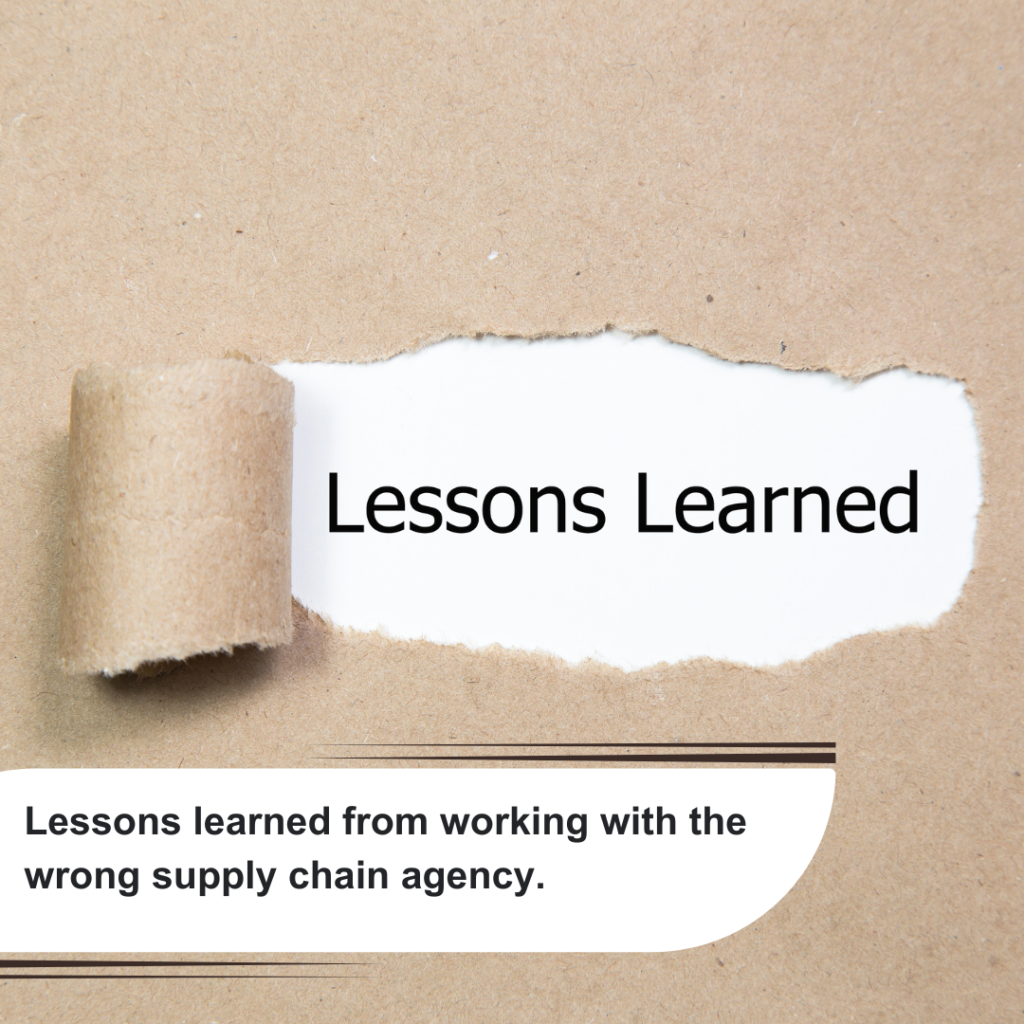
Fear of Inefficiency
One of the primary concerns when working with the wrong supply chain agency is the fear of inefficiency. This can manifest in various ways, such as:
1. Delayed Deliveries: When a supply chain agency is not equipped to handle the volume of orders, it can lead to delayed deliveries, which can have significant consequences for businesses. For instance, a fashion brand may have a new collection launching in a few weeks, but if the supply chain agency fails to deliver the necessary inventory on time, the brand may miss its window of opportunity, resulting in lost sales and revenue.
2. Inaccurate Inventory Management: Inaccurate inventory management can lead to stockouts or overstocking, both of which can be costly and detrimental to business operations. For example, a retailer may order a large quantity of a popular product, only to find that the supply chain agency has mismanaged the inventory, resulting in stockouts and lost sales.
Fear of Quality Issues
Another significant fear when working with the wrong supply chain agency is the fear of quality issues. This can include:
1. Defective Products: When a supply chain agency is not meticulous about quality control, it can lead to defective products reaching the market. For instance, a manufacturer of electronic components may discover that a supplier has shipped defective parts, which can cause costly recalls and damage to the company’s reputation.
2. Non-Compliance with Regulations: Failure to comply with regulations can result in severe consequences, including fines and even legal action. For example, a food manufacturer may find that a supplier has not adhered to food safety regulations, leading to product recalls and significant financial losses.
Fear of Communication Breakdowns
Effective communication is critical in any supply chain partnership. However, when working with the wrong supply chain agency, communication breakdowns can occur, leading to:
1. Misunderstandings and Miscommunication: When there is a lack of clear communication, misunderstandings and miscommunication can arise, leading to delays, errors, and increased costs. For instance, a logistics company may misinterpret a shipment order, resulting in the wrong products being delivered to the wrong location.
2. Inadequate Transparency: Inadequate transparency can lead to a lack of visibility into the supply chain, making it difficult to track products and identify potential issues. For example, a retailer may struggle to track the origin of its products due to inadequate transparency from its suppliers, making it challenging to respond to quality issues or recalls.
Fear of Financial Losses
Lastly, the fear of financial losses is a significant concern when working with the wrong supply chain agency. This can include:
1. Increased Costs: When a supply chain agency is inefficient or ineffective, it can lead to increased costs, including additional labor, transportation, and storage expenses. For instance, a manufacturer may find that a supplier has increased its prices without notice, resulting in higher costs and reduced profit margins.
2. Lost Revenue: In extreme cases, the wrong supply chain agency can lead to lost revenue due to delayed or failed deliveries, stockouts, or product recalls. For example, a retailer may miss its sales targets due to stockouts of a popular product, resulting in lost revenue and a damaged reputation.