In today’s fast-paced business world, supply chain operations play a crucial role in the success of any organization. However, inefficiencies and disruptions in the supply chain can lead to significant financial losses. To avoid this, it’s essential to understand the common pitfalls and implement strategies to optimize your supply chain operations.
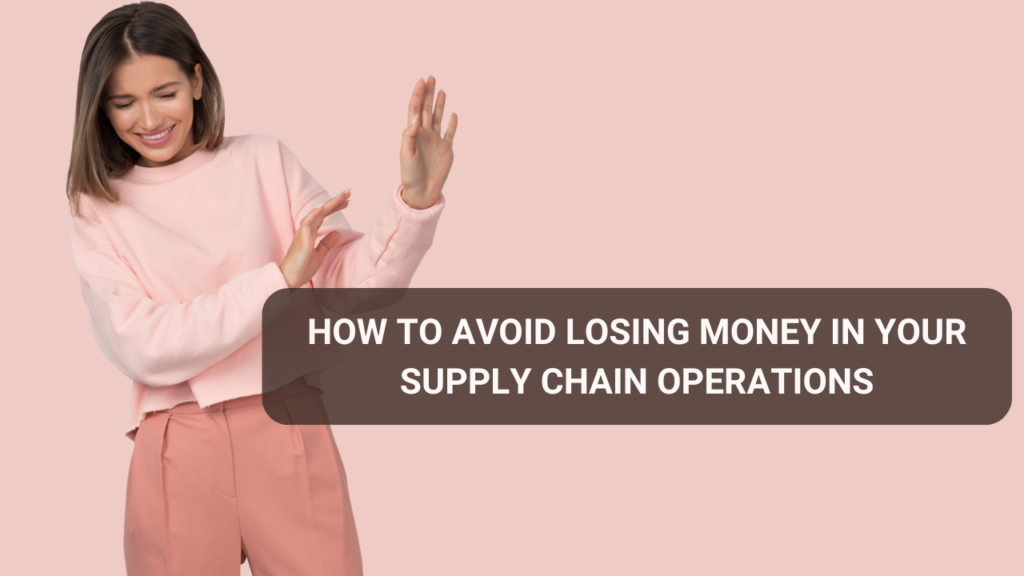
Wasted Time
One of the biggest money-drainers in supply chain operations is wasted time. It’s common for logistics employees to spend at least an hour per day looking for updates on their shipments, which is unnecessary when software can automatically update you on any relevant changes in ETA or ETS. A system like this can save hours of work and allow logisticians to focus on meaningful tasks, like advising partners or talking to potential clients.
For example, if you have two employees spending one hour per day each looking for time changes in shipments, that’s 40 hours of labor per month. In about four months, you end up paying the equivalent of an extra salary. This money could be saved to invest in training, infrastructure, or rewards for your employees to keep up the great work.
Demurrage and Detention Costs
Another way you can lose money in your supply chain is through demurrage and detention costs. A container standing still for too long can result in unnecessary fees. Software solutions can warn you of containers standing idle for an exceptionally long time, preventing these avoidable costs.
Imagine you have a container that incurs $100 per day in demurrage and detention fees. If it sits idle for a week, that’s $700 in lost revenue. By using a system that alerts you when free time is running out, you can take action to avoid these fees and keep your supply chain running smoothly.
Poor Communication
Lastly, poor communication can be a significant source of lost money in your supply chain operations. Logistics software often doesn’t communicate easily with each other, forcing employees to send an overload of emails and documents to partners. This not only wastes time but also increases the risk of human-made errors that can cost thousands of dollars.
By integrating a unified platform, you can visualize your data streams from different software in one place, saving a large amount of time. Furthermore, integrating partners takes only seconds, helping everyone save time when sharing information. By providing partners with transparency, you can enhance your business by quickly building trustworthy relationships and simplifying trade flow management.
Implementing Solutions
The easiest way to stop losing money in logistics operations is by integrating smart software that can simplify the essential work for you. Whether you are wasting time looking for information, getting caught up on demurrage and detention costs, or having trouble communicating with your team and partners, there is a solution that can solve all of these challenges.
For example, ShipBob, a fulfillment company, offers order fulfillment technology with built-in inventory management tools to help you better manage inventory. Their warehouse management system (WMS) allows you to monitor daily operations, track inventory in real-time, and boost productivity to efficiently fulfill orders.
By reducing time on repetitive tasks, gaining visibility on shipments, and collaborating with partners, you will also gain exponential benefits apart from saving money. With the extra time and tools, your employees will make well-informed decisions that will build the basis of a stronger revenue-gaining business.