When it comes to managing a business, supply chain management is a crucial aspect that can make or break the success of an organization. Partnering with the right supply chain agency can ensure a smooth flow of goods and services, while working with the wrong one can lead to significant disruptions and financial losses. In this blog, we will explore five case studies of businesses that were affected by working with the wrong supply chain agency, highlighting the consequences of such partnerships and the importance of careful selection.
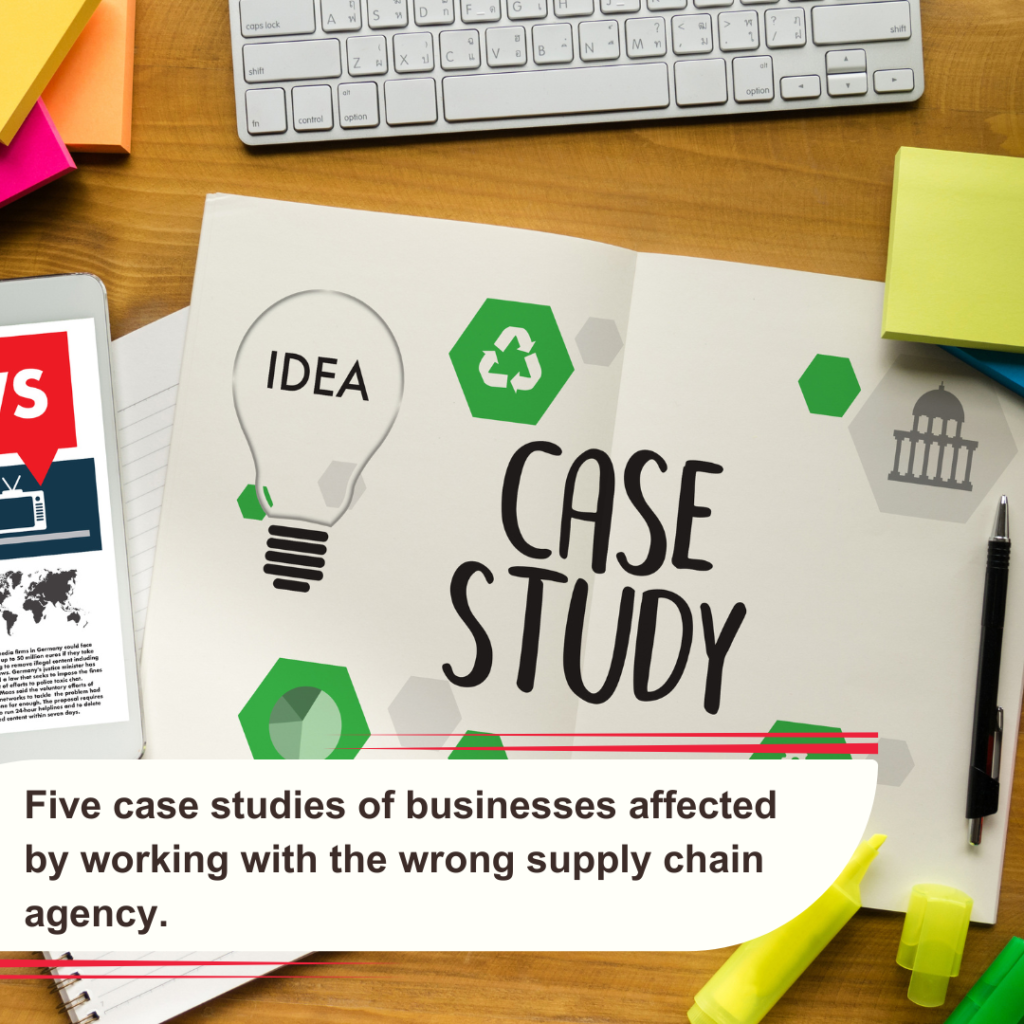
Case Study 1: The Fashion Brand’s Inventory Nightmare
A popular fashion brand, known for its trendy clothing, partnered with a supply chain agency to manage its inventory. The agency promised to streamline the process, but instead, it led to a series of inventory management issues. The agency failed to accurately track inventory levels, resulting in stockouts and overstocking. This caused significant delays in production and distribution, ultimately affecting the brand’s reputation and sales. The brand had to invest additional resources to rectify the situation, including hiring new staff and implementing new inventory management systems.
Case Study 2: The Food Manufacturer’s Quality Control Crisis
A well-known food manufacturer partnered with a supply chain agency to manage its logistics. The agency was responsible for ensuring the timely delivery of raw materials and finished products. However, the agency failed to maintain the required quality standards, leading to contamination and spoilage issues. This resulted in product recalls, damage to the brand’s reputation, and significant financial losses. The manufacturer had to invest in new quality control measures and retrain its staff to ensure compliance with regulatory standards.
Case Study 3: The Retailer’s Supply Chain Disruption
A major retailer partnered with a supply chain agency to manage its supply chain. The agency promised to optimize logistics and reduce costs. However, it failed to do so, leading to frequent stockouts and overstocking. This caused significant disruptions to the retailer’s operations, including delays in restocking shelves and affecting customer satisfaction. The retailer had to invest in new supply chain management systems and re-evaluate its partnership with the agency.
Case Study 4: The Technology Company’s Security Breach
A leading technology company partnered with a supply chain agency to manage its global logistics. The agency was responsible for ensuring the secure transportation of sensitive equipment and data. However, the agency failed to maintain adequate security measures, leading to a data breach that compromised sensitive information. This resulted in significant reputational damage and financial losses. The company had to invest in new security measures and retrain its staff to ensure compliance with regulatory standards.
Case Study 5: The Automotive Manufacturer’s Production Delays
An automotive manufacturer partnered with a supply chain agency to manage its production line. The agency was responsible for ensuring the timely delivery of raw materials and components. However, the agency failed to maintain the required production schedules, leading to frequent delays and production line shutdowns. This caused significant financial losses and affected the manufacturer’s ability to meet customer demand. The manufacturer had to invest in new production management systems and re-evaluate its partnership with the agency.