Supply chain disruptions caused by natural disasters have become a pressing concern for businesses worldwide. From hurricanes to earthquakes, these events can halt production, delay deliveries, and significantly impact a company’s bottom line. In this blog, we will explore current trends in managing these disruptions, focusing on practical examples and strategies that companies are employing to navigate the challenges posed by natural disasters.
Understanding Supply Chain Disruptions
A supply chain is essentially the journey a product takes from raw materials to the consumer. It involves multiple stages, including sourcing, manufacturing, logistics, and distribution. When a natural disaster strikes, it can disrupt any of these stages, leading to delays and increased costs. For instance, during Hurricane Katrina in 2005, many businesses in New Orleans faced severe disruptions as roads and bridges were damaged, halting the transportation of goods and materials.
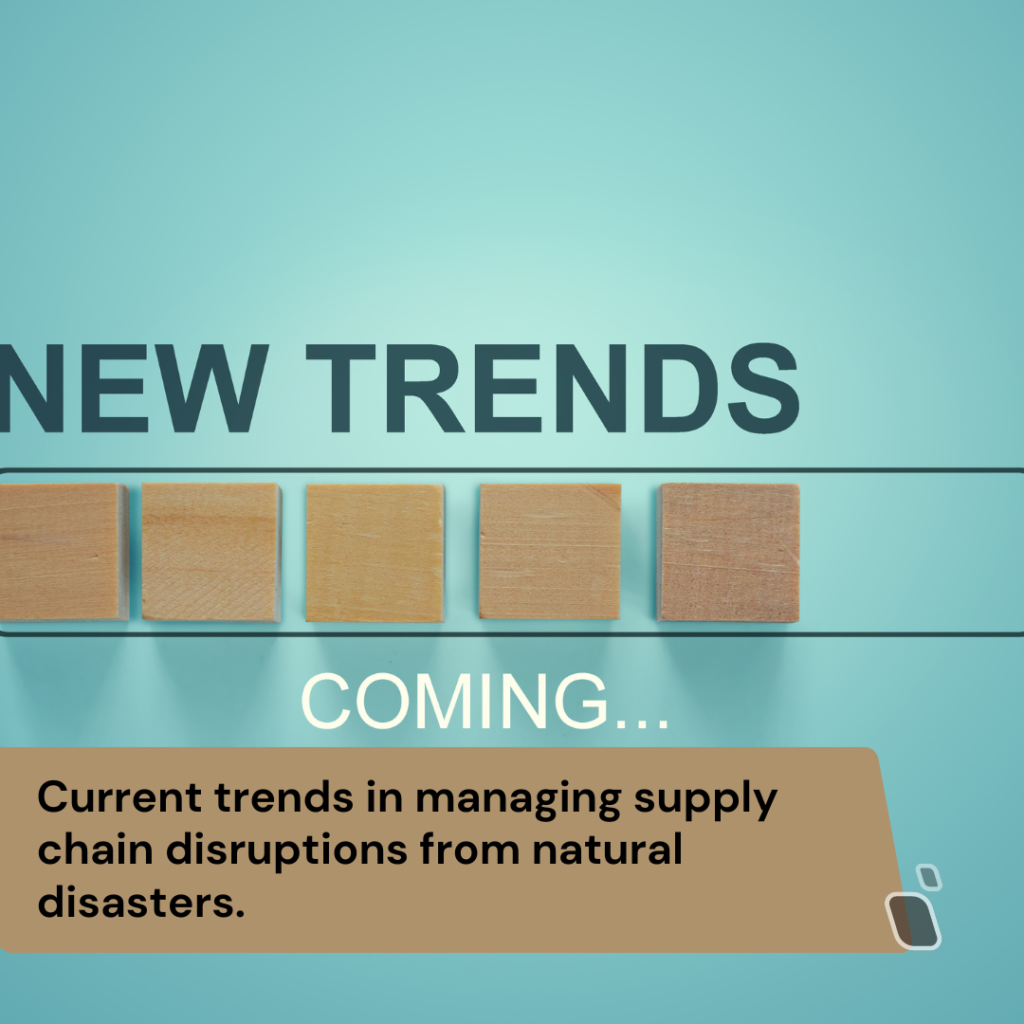
The Ripple Effect of Disruptions
The impact of natural disasters on supply chains can create a ripple effect. For example, if a factory is damaged in an earthquake, not only does that factory halt production, but it also affects suppliers who rely on that factory for components. This can lead to shortages, increased prices, and ultimately, dissatisfied customers. A notable case was the 2011 Thailand floods, which severely disrupted the hard disk drive supply chain, highlighting how interconnected global supply chains can be.
Current Trends in Managing Supply Chain Disruptions
1. Risk Assessment and Preparedness Plans
One of the most effective ways to manage supply chain disruptions is through thorough risk assessment and preparedness planning. Companies are increasingly conducting risk assessments to identify potential vulnerabilities in their supply chains. This involves mapping out critical suppliers, understanding their geographical risks, and developing contingency plans. For instance, companies may establish relationships with multiple suppliers across different regions to avoid dependency on a single source.
2. Building Resilience through Redundancy
Building redundancy into supply chains is another key trend. This means having backup suppliers and alternative logistics options in place. For example, if a company primarily sources materials from a factory in a flood-prone area, it might also establish relationships with suppliers in less vulnerable locations. This strategy ensures that if one supplier is affected, the company can quickly pivot to another source, minimizing disruptions.
3. Real-Time Monitoring and Technology Integration
The integration of technology for real-time monitoring of supply chains is becoming increasingly important. Companies are investing in software that provides visibility into their supply chains, allowing them to track shipments and identify potential disruptions before they escalate. For example, using predictive analytics, businesses can forecast potential risks based on weather patterns and historical data, enabling them to take proactive measures.
4. Collaboration with Suppliers and Stakeholders
Collaboration is essential in managing supply chain disruptions. Companies are working closely with suppliers to ensure they have their own disaster preparedness plans in place. This collaboration can involve sharing information about risks and developing joint contingency plans. For instance, during the COVID-19 pandemic, many companies enhanced their communication with suppliers to navigate the challenges posed by lockdowns and transportation restrictions.
5. Flexibility and Agility in Operations
Flexibility and agility are crucial for companies facing supply chain disruptions. Businesses are adopting agile methodologies that allow them to quickly adapt to changing circumstances. For example, a manufacturer might shift production to a different facility or alter product lines based on available resources and market demand. This adaptability can help mitigate the impact of disruptions and maintain customer satisfaction.
Case Study: Lessons from Natural Disasters
Example: The 2011 Japan Earthquake and Tsunami
The 2011 earthquake and tsunami in Japan had a profound impact on global supply chains, particularly in the automotive and electronics industries. Many companies learned valuable lessons from this disaster. Those that had diversified their supplier base and established contingency plans were better positioned to recover quickly. For instance, some automakers were able to shift production to facilities in other countries, while others faced significant delays due to their reliance on single suppliers in affected areas.
Example: Hurricane Harvey
Hurricane Harvey in 2017 caused widespread flooding in Texas, leading to significant disruptions in the oil and gas supply chains. Companies that had invested in resilient infrastructure and contingency plans were able to minimize downtime. For example, firms that had backup power systems and alternative transportation routes were able to resume operations more quickly than those that did not plan for such contingencies.