When we think of supply chain management, we often imagine a seamless process where goods are manufactured, transported, and delivered to our doorstep without a hitch. However, the reality is that supply chain failures can have devastating consequences, from delayed shipments to financial losses. In this blog, we’ll delve into the inner workings of a bad supply chain agency and explore the common pitfalls that can lead to these issues.
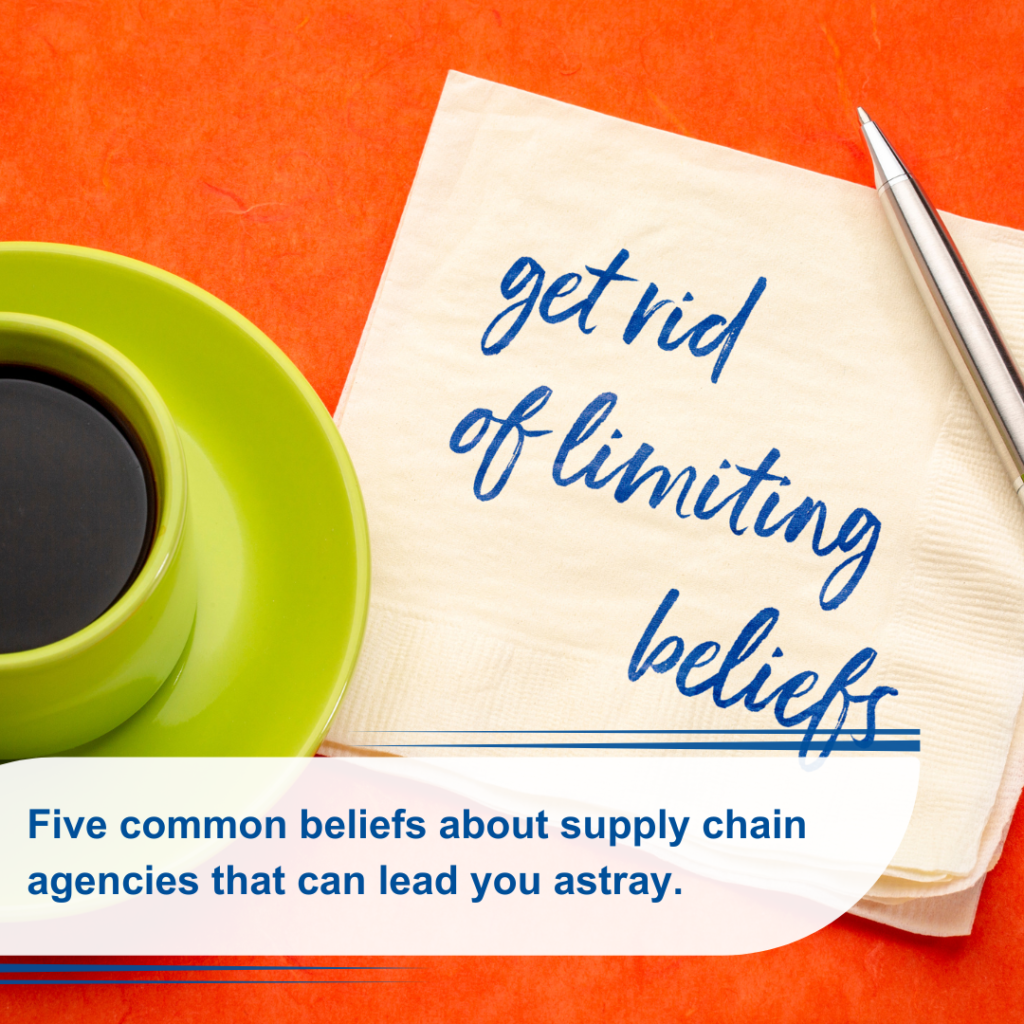
Lack of Visibility and Communication
One of the primary reasons supply chain failures occur is due to a lack of visibility and communication among stakeholders. Imagine a scenario where a manufacturer produces a batch of products, but the supplier fails to notify the logistics company about the shipment. As a result, the logistics company is unaware of the shipment and cannot plan accordingly, leading to delays and potential losses.
For instance, consider a company called “GreenTech” that specializes in eco-friendly cleaning products. GreenTech outsources its manufacturing to a supplier, “EcoClean,” which produces the products in a factory located several hours away. EcoClean fails to notify the logistics company, “LogiTech,” about the shipment, causing LogiTech to be unaware of the products and unable to plan for their transportation. This lack of communication leads to a delay in the delivery of the products, causing GreenTech to miss its sales targets and incur additional costs.
Inefficient Inventory Management
Another common issue in supply chain management is inefficient inventory management. When inventory levels are not properly managed, it can lead to stockouts, overstocking, and wasted resources.
For example, let’s consider a company called “FashionFrenzy” that sells trendy clothing. FashionFrenzy outsources its manufacturing to a supplier, “StyleHouse,” which produces the clothing in a factory located overseas. StyleHouse fails to accurately track inventory levels, leading to stockouts of popular items. As a result, FashionFrenzy is unable to fulfill customer orders, causing a loss of sales and revenue.
Inadequate Risk Management
Supply chain agencies must also be prepared to manage risks that can impact their operations. This includes natural disasters, political unrest, and economic downturns. When a supply chain agency fails to adequately manage these risks, it can lead to significant disruptions and losses.
For instance, consider a company called “TechCorp” that manufactures electronic components. TechCorp outsources its manufacturing to a supplier, “ComponentCo,” which produces the components in a factory located in a region prone to natural disasters. When a hurricane hits the region, ComponentCo’s factory is damaged, causing a disruption in the supply chain. TechCorp is unable to fulfill customer orders, causing a loss of sales and revenue.
Inadequate Quality Control
Finally, supply chain agencies must ensure that the products they source meet the required quality standards. When a supply chain agency fails to implement adequate quality control measures, it can lead to the delivery of low-quality products, which can damage the agency’s reputation and lead to financial losses.
For example, consider a company called “FoodFusion” that sources food products from various suppliers. FoodFusion outsources its quality control to a third-party agency, “QualityCheck,” which fails to properly inspect the products. As a result, FoodFusion delivers low-quality products to its customers, causing a loss of sales and revenue.