A three-step process to prevent money loss in your supply chain, written in layman’s language with an example:
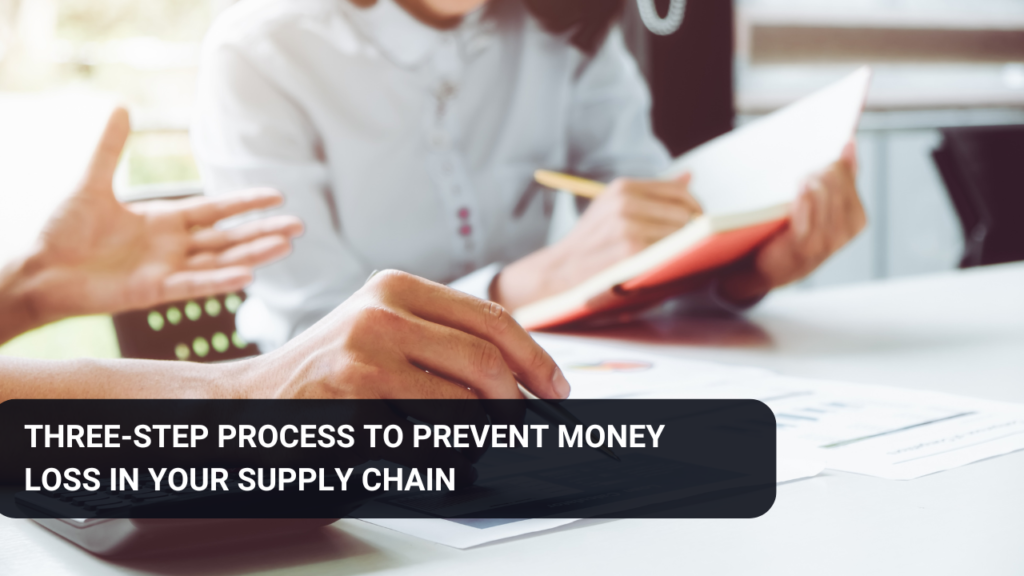
3 Simple Steps to Plug Money Leaks in Your Supply Chain
Does it feel like money is slipping through the cracks in your supply chain? You’re not alone. Many businesses struggle with supply chain inefficiencies that bleed profits. But there are steps you can take to plug those leaks and keep more of your hard-earned cash.
Here’s a simple 3-step process to prevent money loss in your supply chain:
1. Identify Weak Points
The first step is to pinpoint where you’re losing money. Look for bottlenecks, delays, and inefficiencies throughout your supply chain. Some common culprits include:
– Excess inventory sitting in warehouses
– Damaged goods and product returns
– Inefficient transportation routes
– Lack of supply chain visibility and data
For example, let’s say you run an apparel company. You notice a lot of your inventory is getting stuck in customs for weeks, delaying shipments to retailers. This creates a backlog and forces you to offer discounts to clear out old stock. That’s a major source of lost revenue.
2. Optimize Processes
Once you’ve identified the weak points, look for ways to optimize those processes. Implement lean manufacturing principles, automate repetitive tasks, and streamline workflows. Some strategies include:
– Implementing just-in-time inventory management
– Investing in supply chain visibility software
– Renegotiating contracts with suppliers and carriers
– Conducting regular audits and process improvements
Continuing the apparel example, you could look into getting expedited customs clearance for your goods. You might also reroute shipments through a different port to avoid congestion. Optimizing the customs process will reduce delays and minimize discounted sales.
3. Measure and Monitor
The final step is to measure the impact of your improvements and monitor for new issues. Track key performance indicators (KPIs) like on-time delivery rates, inventory turnover, and total supply chain costs. Regularly review these metrics to spot trends and identify areas needing further optimization.
It’s also important to have a plan for responding quickly to supply chain disruptions. Maintain strong relationships with suppliers and carriers, and have contingency plans in place for alternate sourcing and transportation options.
Continuing the example, you might set up automated alerts to notify you of any customs delays. That way you can proactively reach out to retailers, adjust production schedules, and take other steps to minimize the impact. Monitoring KPIs and having a rapid response plan will help you stay on top of supply chain issues before they spiral out of control.